Our clients industrial projects are increasingly becoming more complex: supply chains are international with suppliers located everywhere worldwide, far from their production sites and from the final destination of the products sold to their customers.
This complexity requires the ability to track every single component or sub-module of an industrial project, to monitor all suppliers orders and to provide merge in transit consolidation of all components on a single agreed packing platform, at the right time before delivery to the worksite of the final customer.
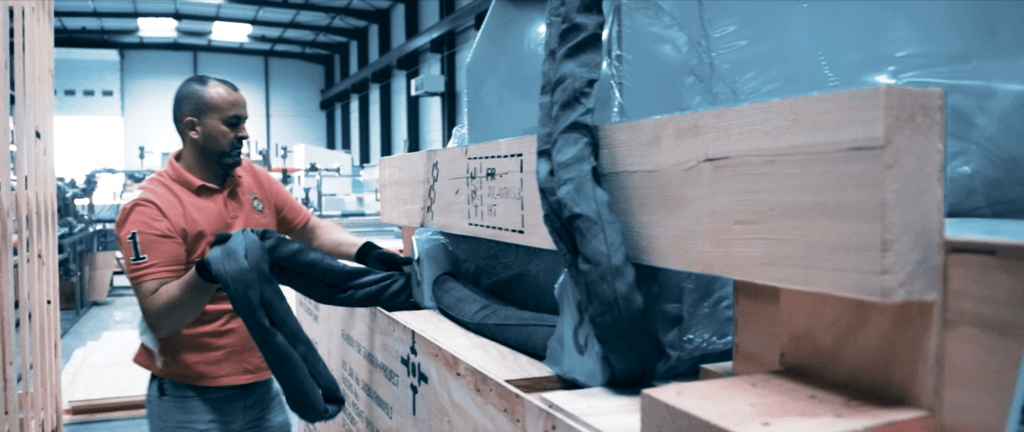
Material flow monitoring
As we work upstream the export packing phase, we deliver a complex monitoring of dozens of components, sourced everywhere across the world in order to synchronise the deliveries to our storage and packing sites used by our clients as an opportunity to merge in transit their orders.
Our customers’ orders are uploaded in our project management software and are managed proactively by our team to chase suppliers about the expected delivery dates to our platforms. We send several reminders to suppliers and alert our customers when a delay is expected on each component (exception management).
Up to 11 client references can be managed in our system and especially :
– Project number
– Product code or SKU number
– Product description
– SKU quantity
– Each part serial number
– Barcode number
– Carton or crate number (each SKU being linked to a carton/crate number)
– Shipping number (or transport document number)
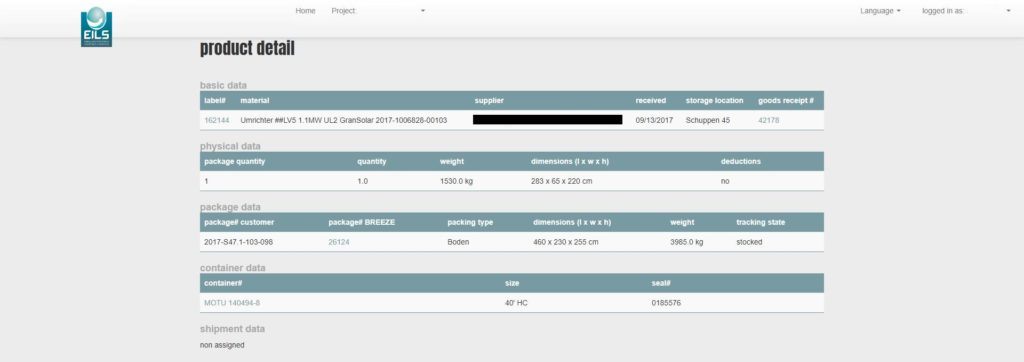
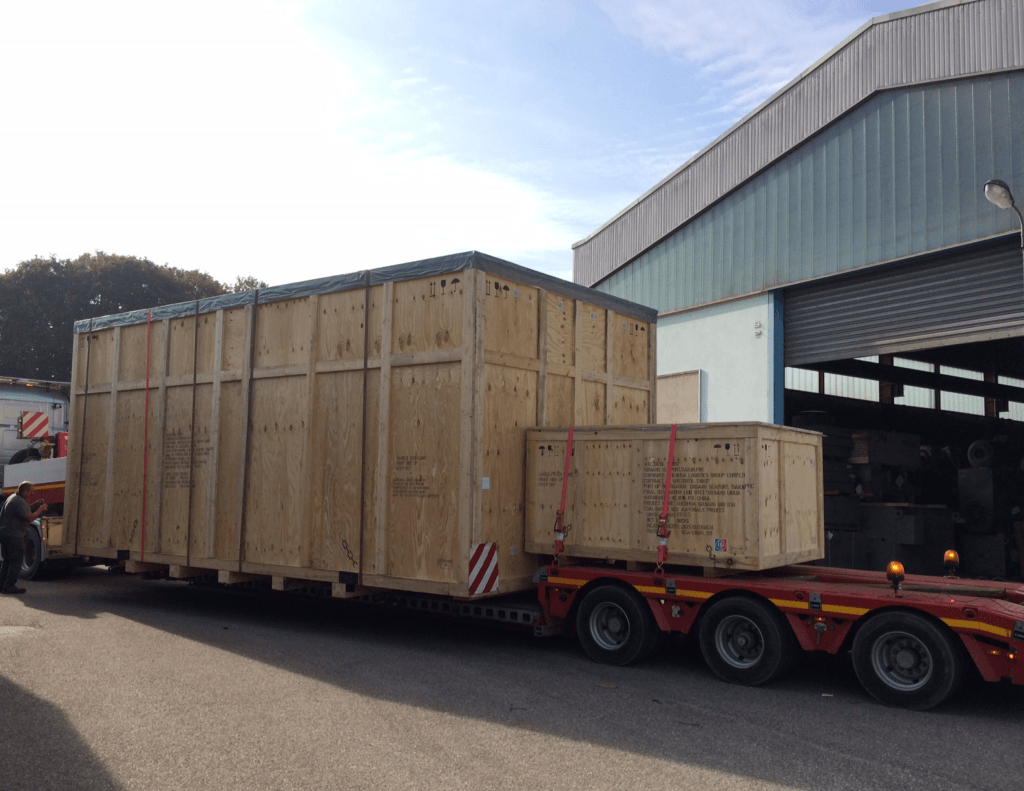
When components are delivered on our operations sites, our team execute receiving controls for each product or part. We send alerts to our customers regarding any non-conformance and consolidate parts by packing units. We then execute the product labelling and the packing before issuing the detailed packing lists of each shipment.
Then shipments are prepared with transport companies or freight forwarders nominated by our customers up to departure of the goods.